The Detailed Technological Process of Enamel Production
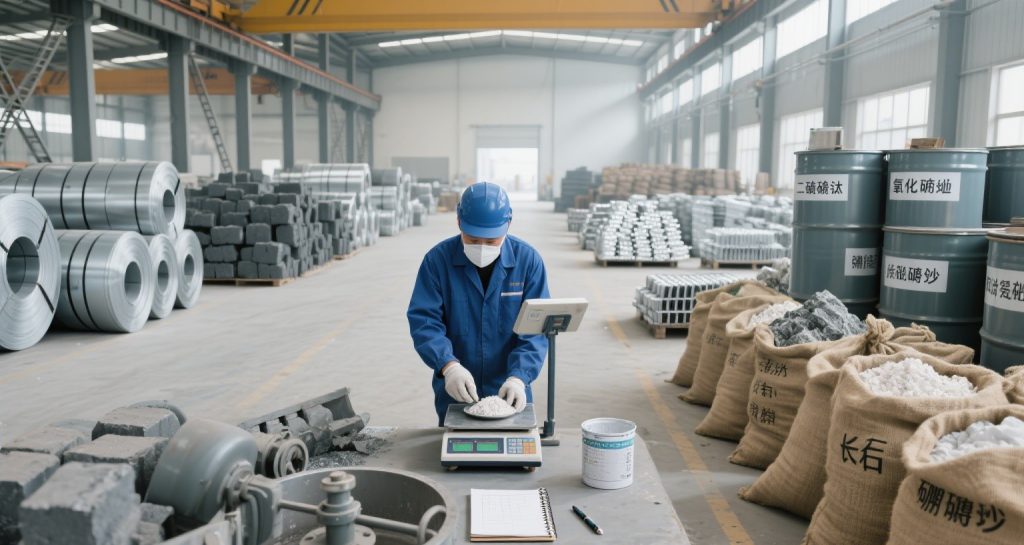
Enamel production is a complex industrial process involving multiple procedures and multidisciplinary knowledge. Its core lies in firmly attaching inorganic vitreous materials to the surface of metal substrates through high-temperature melting, thereby creating composite products with excellent properties such as aesthetic appeal, corrosion resistance, and wear resistance. The following is a detailed technological process of enamel production:
1. Raw Material Preparation
- Metal Substrate Materials: Commonly used metal substrate materials include steel plates, cast iron, aluminum, etc. Steel plates are widely applied in daily-use enamel products and industrial enamel products due to their good formability and strength. Cast iron is often used for manufacturing large industrial equipment and cookware. Aluminum substrates, on account of their light weight and good thermal conductivity, are suitable for some special-purpose enamel products. The quality of metal substrates directly affects the final performance of enamel products. Therefore, when selecting them, their chemical composition, mechanical properties, and surface quality need to be strictly controlled.
- Enamel Glaze: Enamel glaze is mainly composed of vitreous raw materials (such as quartz, feldspar, borax, etc.), fluxes (such as soda ash, potassium carbonate, etc.), colorants, opacifiers (such as titanium dioxide, antimony oxide, etc.), and other additives (such as adhesion promoters, defoamers, etc.). According to different usage requirements and metal substrate materials, the glaze formula needs to be precisely adjusted. For example, for enamel products in contact with food, the heavy metal content in the glaze must be strictly controlled to ensure food safety. The preparation process of the glaze includes steps such as weighing, mixing, melting, quenching into granules, and grinding of raw materials, ultimately producing glaze slurries or dry glaze powders that meet the requirements.

2. Blanking
According to the design requirements of products, metal substrates are processed into the required shapes through processes such as stamping, stretching, welding, and casting. For example, when producing enamel basins, the stamping process is usually adopted to stamp steel plates into basin shapes. For enamel pipe fittings with complex shapes, welding or casting methods may be required for molding. During the blanking process, attention should be paid to controlling the dimensional accuracy, surface flatness, and shape regularity of the substrates to avoid defects such as cracks, air holes, and burrs, as these will affect the subsequent enamel quality.
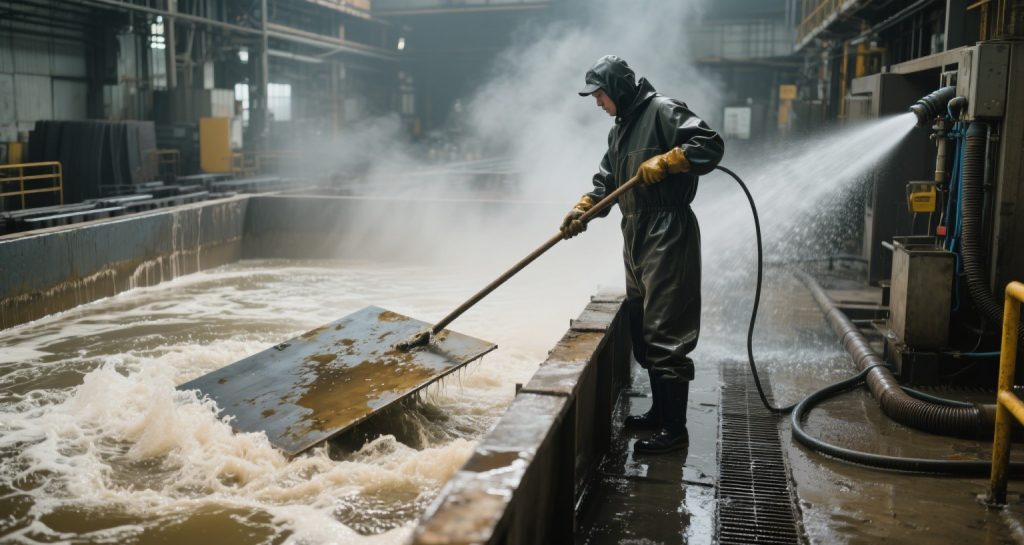
3. Surface Treatment
- Cleaning: The surface of the metal after blanking often adheres to impurities such as oil stains, rust, and dust, which must be thoroughly cleaned. Cleaning usually uses alkaline cleaners, acidic cleaners, or organic solvents to remove surface dirt through methods such as immersion, spraying, and ultrasonic treatment. For example, for steel plate substrates with a large amount of oil stains, alkaline cleaners can be used for degreasing treatment first, and then rinsed thoroughly with clean water.
- Rust Removal: If there is rust on the metal surface, rust removal treatment is required. Common rust removal methods include mechanical rust removal (such as sandblasting, polishing) and chemical rust removal (such as pickling). Sandblasting uses the impact of high-speed sand flow to clean and roughen the metal surface. While removing rust and impurities, it can also increase the surface roughness and improve the adhesion between the enamel glaze and the metal substrate. Pickling dissolves and removes rust through a chemical reaction between the acid solution and the rust. After rust removal, the metal surface should present a uniform and clean metallic luster.
- Activation Treatment: In order to further improve the bonding force between the enamel glaze and the metal substrate, the metal surface after cleaning and rust removal usually needs to be activated. For example, an oxidation treatment is carried out on the surface of the steel substrate to form an extremely thin oxide film. This oxide film can chemically react with the components in the enamel glaze, enhancing the adhesion between the two. For aluminum substrates, surface treatment methods such as anodizing can be used.
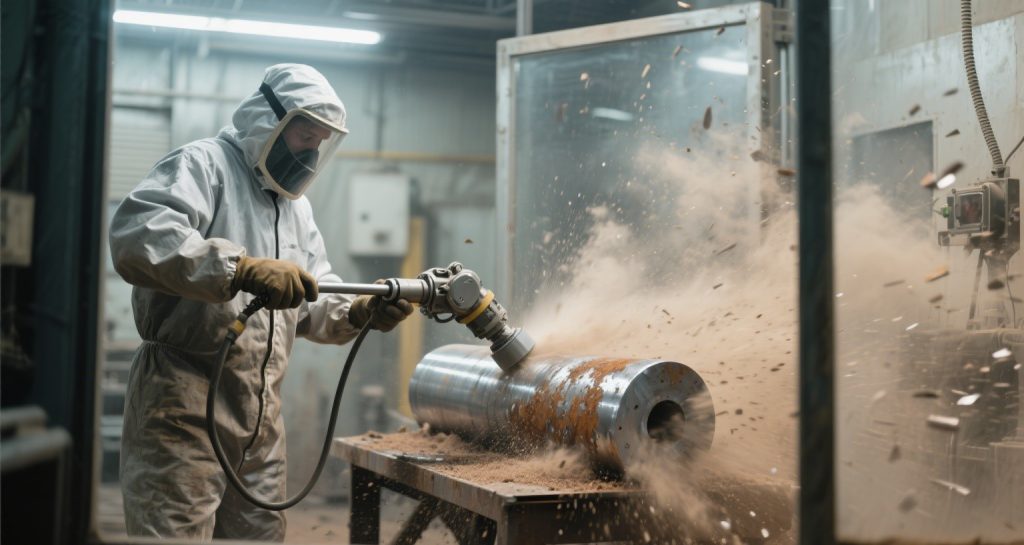
4. Glazing
Glazing is the process of uniformly coating the prepared enamel glaze on the surface of the metal substrate that has undergone surface treatment. According to the characteristics of products and production requirements, the main glazing methods are as follows:
- Dipping Method: Immerse the metal substrate into the glaze slurry, and then slowly take it out to make the glaze slurry adhere evenly to the surface of the substrate. The dipping method is simple to operate and is suitable for enamel products with simple shapes and uniform surface requirements, such as enamel bowls and basins. However, for products with complex shapes or deep holes and grooves, problems such as uneven glaze layer thickness may occur.
- Spraying Method: Use a spray gun to spray the glaze slurry or dry glaze powder onto the surface of the metal substrate in the form of mist. The spraying method can precisely control the glaze layer thickness and is suitable for enamel products of various shapes, especially for large or complex workpieces. By adjusting parameters such as the pressure of the spray gun, the size of the nozzle, and the spraying distance, glaze layers of different thicknesses and effects can be obtained.
- Powder Sprinkling Method: Evenly sprinkle the dry glaze powder on the preheated surface of the metal substrate, and use the residual heat of the substrate to partially melt and adhere the glaze powder. The powder sprinkling method is often used for manufacturing enamel products with special decorative effects, such as artistic enamel and cloisonné handicrafts.
- Electrostatic Spraying Method: Apply a high-voltage electrostatic field between the spray gun and the metal substrate to make the glaze powder charged. Under the action of electrostatic attraction, the glaze powder is evenly adsorbed on the surface of the metal substrate. The electrostatic spraying method has the advantages of uniform glaze layer, high coating utilization rate, and low pollution, and is widely used in industrial production.
No matter which glazing method is used, it is necessary to ensure that the glaze layer is uniform, free of bubbles and omissions, and the thickness of the glaze layer should be well controlled. If the glaze layer is too thin, it will affect the corrosion resistance and decorative effect of the product. If the glaze layer is too thick, problems such as porcelain explosion and peeling are likely to occur during the firing process.
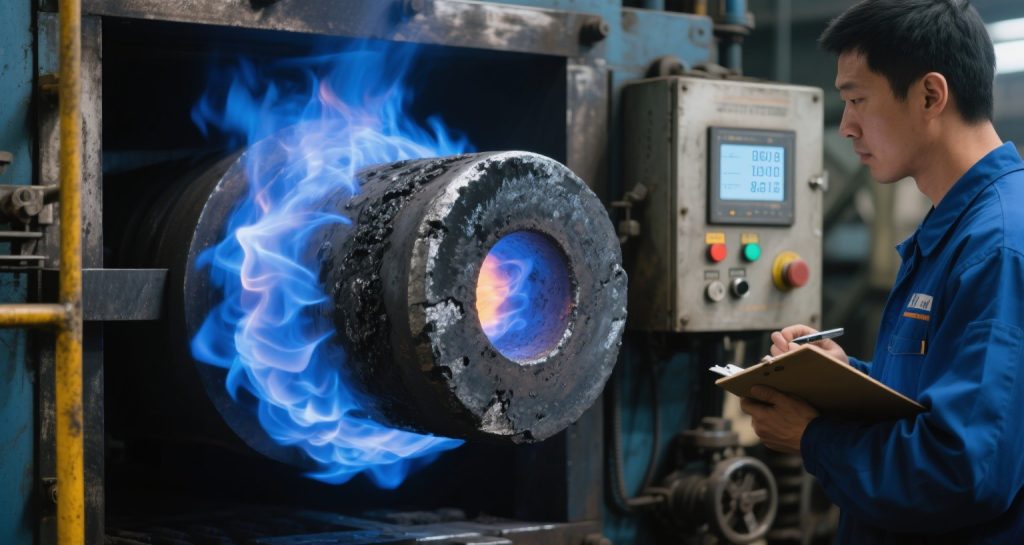
5. Firing
The glazed products need to be fired at high temperature to melt the enamel glaze and firmly bond it with the metal substrate. The firing process is generally carried out in tunnel kilns, shuttle kilns, or rotary kilns. Different kiln types are suitable for different production scales and product requirements. The firing temperature and time are determined according to the glaze formula and metal substrate material. Generally, the firing temperature ranges from 800°C to 950°C, and the firing time ranges from a few minutes to dozens of minutes.
During the firing process, the enamel glaze undergoes a series of complex physical and chemical changes. First, the moisture and volatile substances in the glaze evaporate. Then, the glaze gradually melts and levels under the action of surface tension. Subsequently, the glaze chemically reacts with the surface of the metal substrate, forming chemical bonds and mechanical interlocking to achieve a firm combination. During the firing process, the temperature curve and atmosphere in the kiln need to be strictly controlled. Avoid problems such as too high or too low temperature, too fast or too slow heating rate, otherwise, defects such as bubbles, pinholes, scale explosion, and porcelain detachment will occur on the glaze surface.
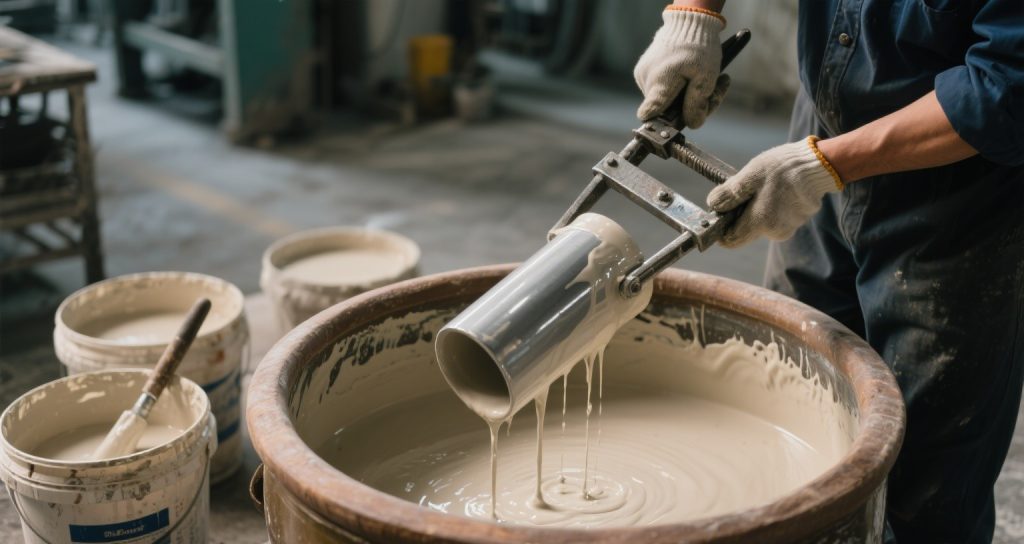
6. Decoration and Post-treatment
- Decoration: In order to improve the aesthetics and artistry of enamel products, decorative treatment can be carried out on the fired products. Common decorative methods include color decoration, decal application, spray painting, carving, etc. Color decoration uses colored glazes to paint patterns or characters on the glaze surface, and then undergoes secondary firing to make the colored glaze blend with the original glaze surface. Decal application involves pasting pattern-printed decals on the glaze surface, and after firing, the patterns on the decals are transferred to and combined with the glaze surface. Spray painting uses a stencil and a spray gun to spray colored glaze onto the glaze surface to form patterns. Carving creates various patterns and designs on the glaze surface through mechanical or chemical methods.
- Post-treatment: Sometimes, decorated enamel products also need to undergo some post-treatment processes, such as polishing, glazing, and coating protection. Polishing can make the glaze surface smoother and brighter, improving the texture of the product. Glazing treatment can increase the gloss and wear resistance of the glaze surface. Coating protection involves applying a transparent protective coating on the glaze surface to further enhance the corrosion resistance and service life of the product.
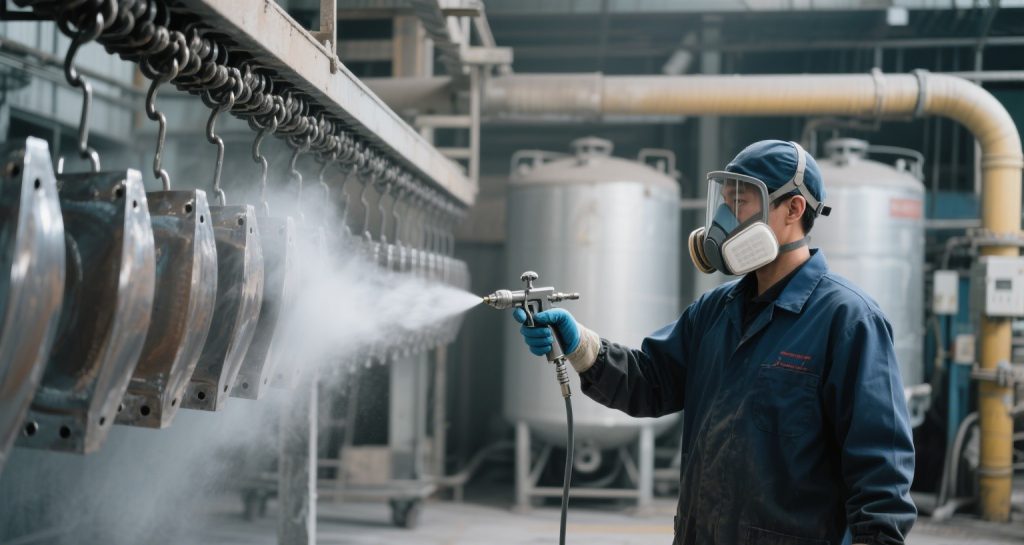
7. Quality Inspection
After the production of enamel products is completed, strict quality inspection is required to ensure that the products meet relevant standards and customer requirements. Quality inspection items mainly include appearance quality inspection, physical property inspection, and chemical property inspection.
- Appearance Quality Inspection: Visually inspect whether the surface of the enamel product is flat and smooth, and check for defects such as bubbles, pinholes, cracks, porcelain detachment, and color difference. Also, check whether the patterns and characters are clear and accurate, and whether the decorative effect meets the requirements.
- Physical Property Inspection: It includes hardness testing, wear resistance testing, impact resistance testing, etc. Hardness testing usually uses a Mohs hardness tester or a Rockwell hardness tester to detect the hardness of the glaze surface. Wear resistance testing uses a specific friction device to simulate the wear situation in actual use and evaluate the wear resistance of the glaze surface. Impact resistance testing drops a steel ball of a certain weight from a specified height onto the product surface to check whether there is damage, peeling, etc. on the glaze surface.
- Chemical Property Inspection: It mainly detects the corrosion resistance, acid and alkali resistance, heavy metal leaching amount, etc. of enamel products. Corrosion resistance testing immerses the product in a specific corrosive medium and observes the corrosion of the glaze surface. Acid and alkali resistance testing places the product in acidic and alkaline solutions respectively to test the stability of the glaze surface in acid-base environments. Heavy metal leaching amount detection is aimed at enamel products in contact with food, to detect whether the leaching amount of heavy metals (such as lead, cadmium, etc.) under specific conditions meets food safety standards.
Only enamel products that pass the quality inspection can enter the packaging and delivery process. Unqualified products need to be reworked or scrapped according to the specific situation.
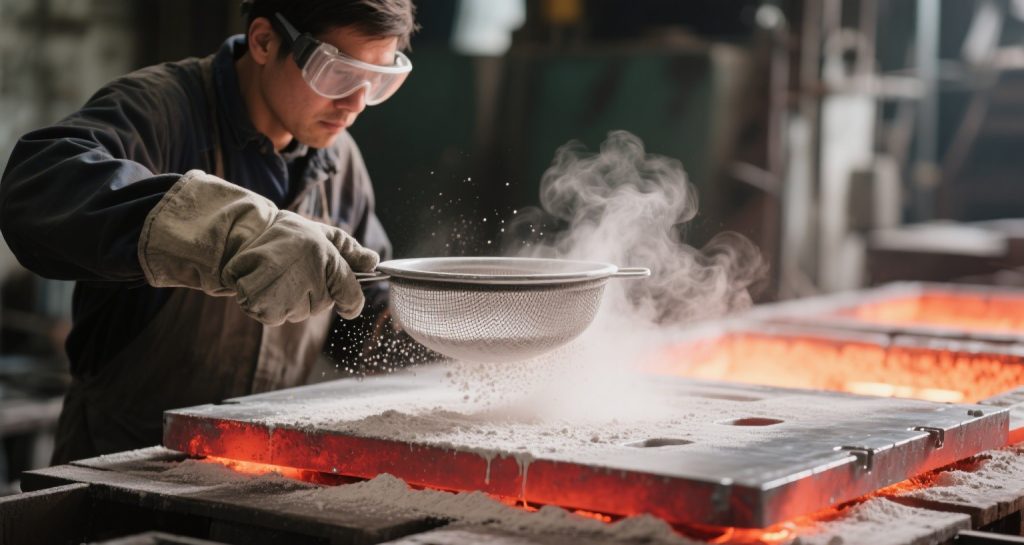
8. Packaging and Delivery
According to the characteristics of products and transportation requirements, select appropriate packaging materials and packaging methods to package enamel products. Commonly used packaging materials include cartons, foam plastics, bubble films, etc. During the packaging process, attention should be paid to protecting the product surface to avoid damage such as collision and scratching during transportation and storage. After the packaging is completed, the products can go through the delivery procedures and enter the sales and circulation links only after passing the inspection.
The above covers the main processes of enamel production. If you want to have a deeper understanding of a certain process or have other specific requirements, feel free to let me know.
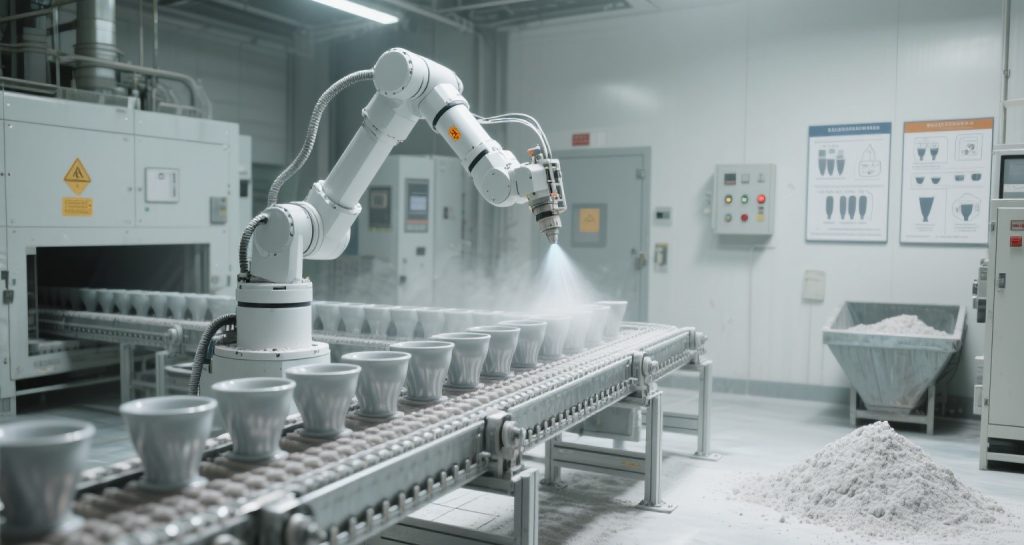
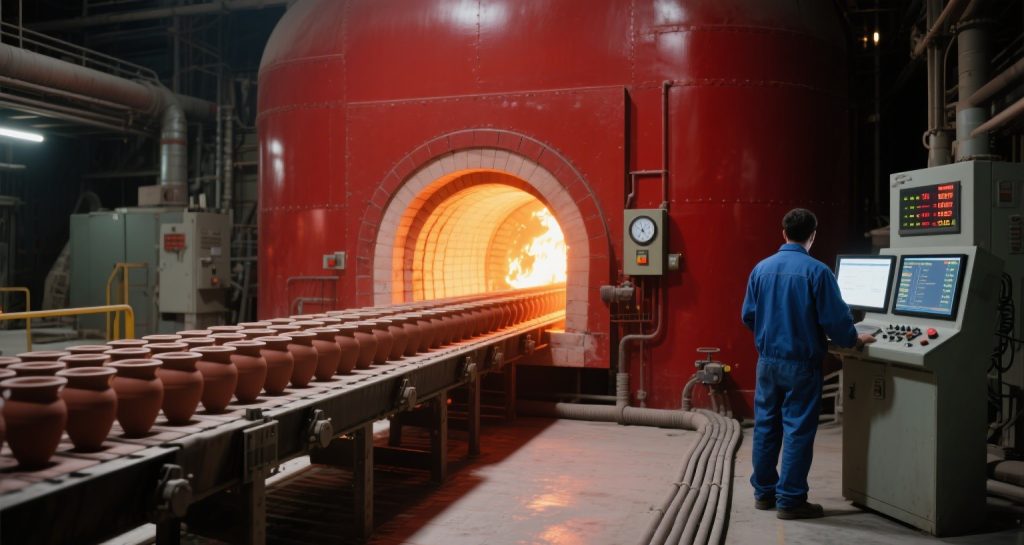
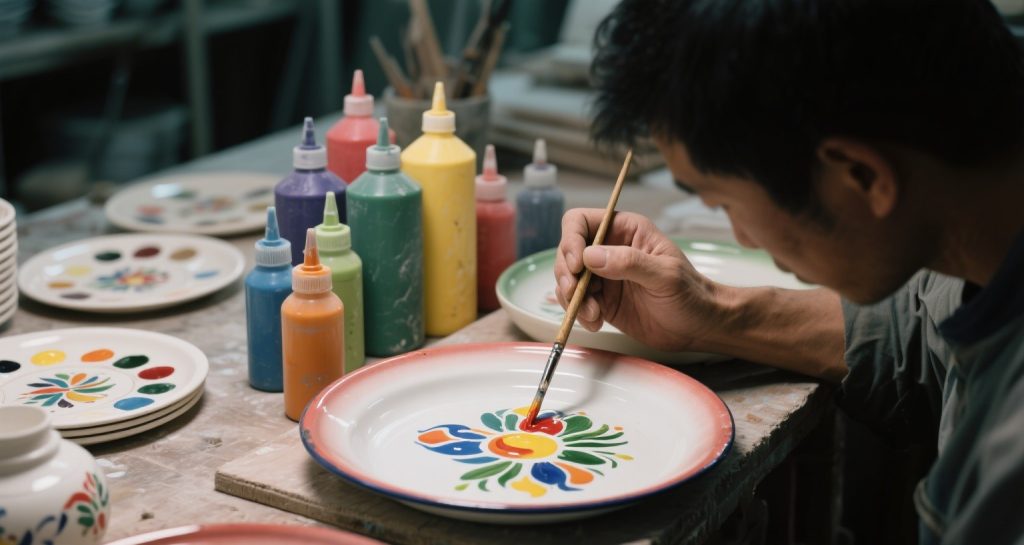
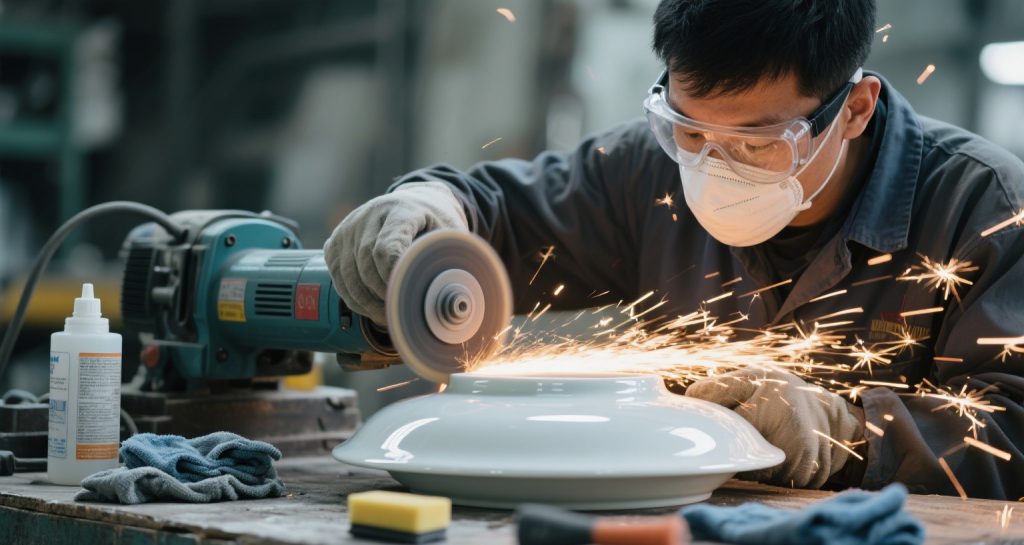